
Our commitment to providing a safe, high-quality product touches every part of our process – from our choice of raw materials for each candle to our final packaging and shipping to your door.
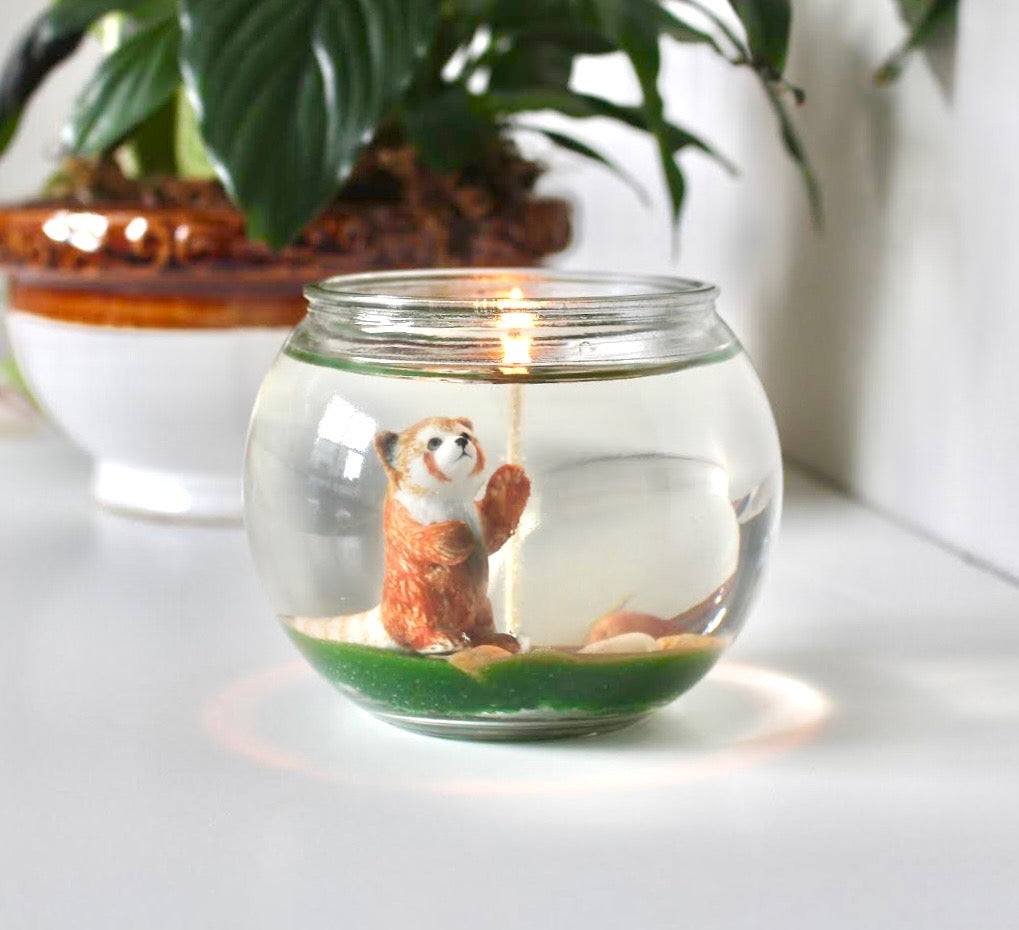
Our candle gel is the Penreco Versagel™ brand. These gels are specially formulated for candle making and offer flash points of 450°F and a (typical) sustained burn (Fire Point) of 500°F. Zinc cored wicks are used in our candles because they stand straight in hot gel during production and burning. Wick length and placement are calculated carefully for each candle. Our fragrances are high-quality and meet all health and safety standards as set by the International Fragrance Association (IFRA). Our candle scents have been tested and are compatible with gel candles when used according to Penreco’s guidelines. Our candles are designed to enhance, but not overpower, your space with aroma.
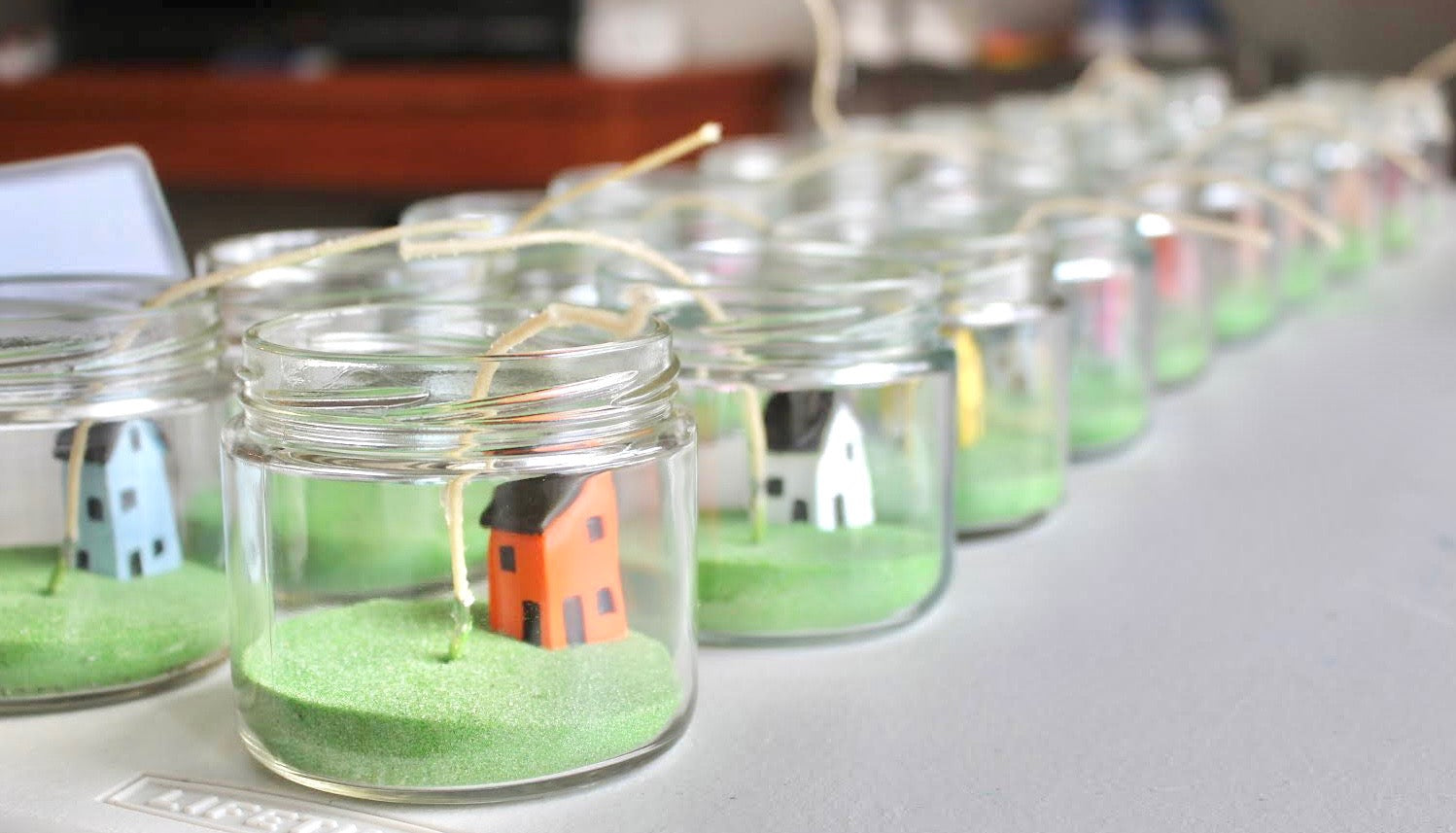
Our candles are individually hand-poured in our West Chester, Ohio studio to ensure the highest quality product. We melt the wax at a low temperature, add in color, and mix-in the measured fragrance. The wax then solidifies in a warm oven to reduce bubbling. Further baking may be needed depending on the amount of bubbles desired per candle. Once cooled, each candle is personally inspected to check for wax quality and pour and fragrance consistency. The tops are smoothed over with heat, the vessels wiped clean, and labeled by hand. We use environmentally friendly packaging wherever possible and ensure that your candle reaches you in perfect condition with our proven packaging standards.
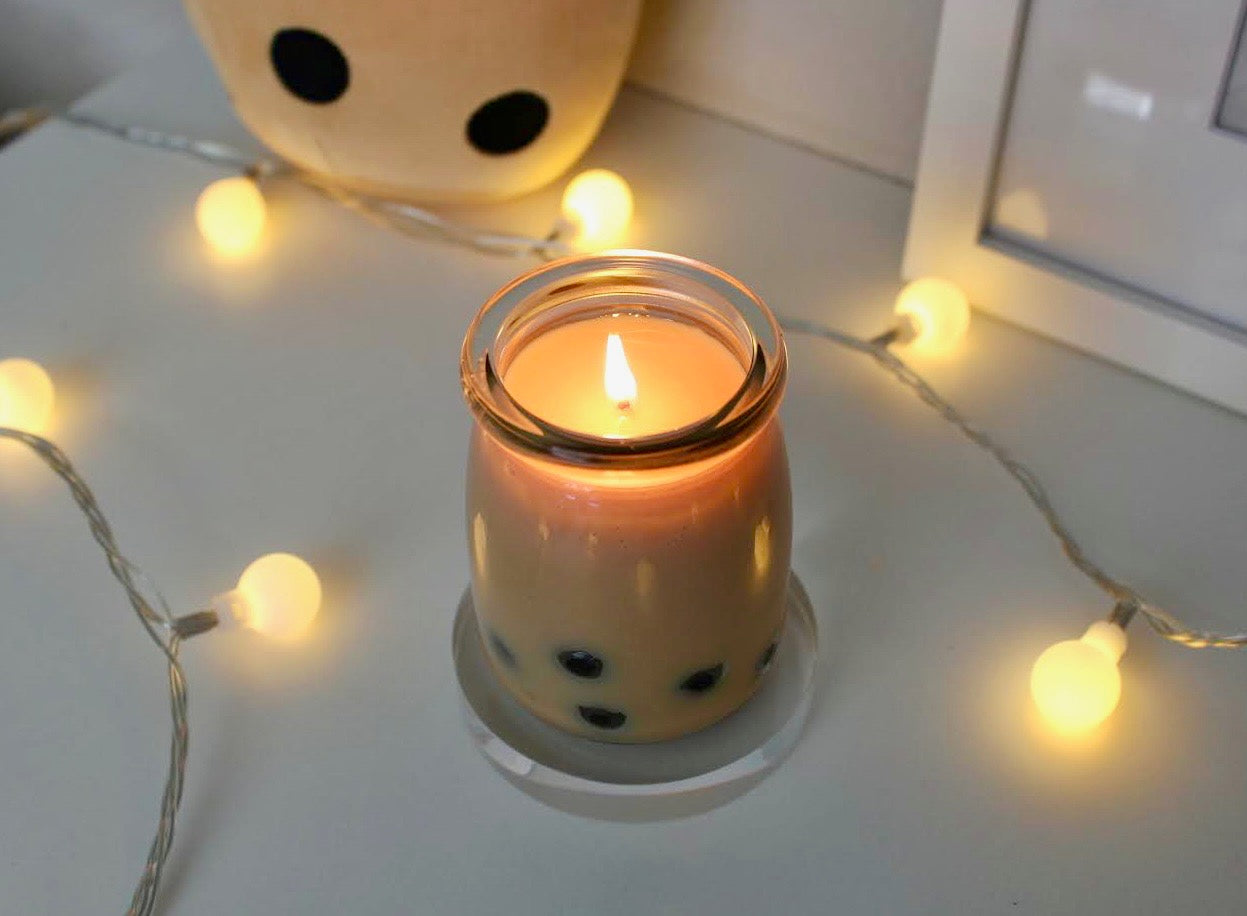
It is our top priority to produce a safe candle. We have spent many hours of extensive research and experimentation to ensure that each candle is finished beautifully and is a delight to receive. We rigorously test our candles to ensure that each and every candle we make offers a fragrant, safe, and long-lasting candle experience for our customers.
Burn Test
A “burn test” is conducted on each of our candles. Burn testing is the process of evaluating finished candles for performance from the first to the last burn. The goal is to ensure that our candles burn at a normal rate, are not producing an abnormal amount of soot, and are safe for the end-user. The individual components of our candles—the type of wax, fragrance oil, fragrance load, candle dyes, wick choice, container diameter and shape—all factor into how our candles burn. Every formula we create is burn tested before selling to customers.
2. We then place the candle on a clean, flat, heat resistant surface. We always conduct the Burn Test within our work-space, as candles should never be left unattended while lit. It is critical we keep an eye on the testing candle, especially if we are using a new wick.
3. The candle is then lit and the time is recorded.
4. After 2 hours, we record the details of the melt pool and the wick appearance. The melt pool is measured and we note if we achieved the desired diameter. We also record the release of soot or mushrooming of the wick.
5. After 4 hours, the details of the melt pool and wick are recorded again, and the flame is gently extinguished. We again measure the diameter of the melt pool, and in addition we measure the depth. A melt pool with ½” depth is desired. If the wick is mushrooming and soot is being released, the melt pool is likely deeper than ½” and our wick size needs to be re-evaluated.
6. We then allow the candle to cool for at least 5 hours before steps 3, 4, and 5 are repeated until the candle is completely burned. The quality of the burn is assessed throughout the process to make sure we are seeing exactly what our customers will see.